コネクタは複数のピンや端子を有し、正確な電気的接続と機械的安定性が求められる部品ですが、通常のはんだ付けでは酸化膜の強い金属端子に対して濡れ不良が起こりやすく、フラックス残渣の除去や高温加熱による熱ダメージといった課題があります。
これに対し、超音波はんだ付けでは超音波振動により端子表面の酸化膜を効果的に除去でき、フラックスを使わない低温条件でも高い濡れ性が得られます。そのため、端子間隔が細かいコネクタでも余分なはんだブリッジを低減しながら強固な接合を形成でき、後処理工程も簡素化されるため、生産効率と信頼性の向上が同時に実現しやすくなります。
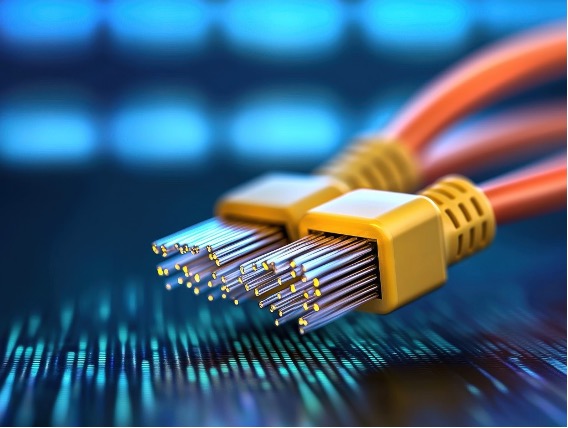
以下のようなケースでは、通常のはんだ付けよりも超音波はんだ付けが有効となります。
フラックス残渣が問題となる場合
- 医療機器や真空装置など、端子部への化学物質残留が厳しく規制されている用途。
- 洗浄工程が複雑・高コストとなる製造ライン。
酸化膜が強固なコネクタ端子材料を使用している場合
- アルミニウムやステンレス、ニッケルメッキなど、フラックスだけでは十分除去できない酸化皮膜が生じやすい金属。
- 異種金属同士の組み合わせで通常のはんだ付けが不安定な場面。
低温接合が必須となる場合
- コネクタ樹脂ボディや近接する樹脂部品が熱に弱い場合。
- 高密度実装基板で隣接部品に熱影響を最小限に抑えたい環境。
高い信頼性・長期安定性が要求される場合
- 自動車や産業機器など、振動や温度変化の激しい環境で使用されるコネクタ。
- ボイド(空隙)が少なく、冶金的に安定した接合を形成したい場合。
リソー技研の超音波はんだ技術にご期待下さい
当社では、超音波はんだ装置製造のパイオニアとして、様々な製品を取り扱っております。ハンディタイプのはんだごてから、量産専用の完全オーダーメイドの自動化装置まで、様々なご要望にお応えしております。